Problem solving process lean - Problem Solving :: Lean Six Sigma Experts Community
Commonly Used Lean Tools and Approaches. A3 Problem - Solving. This 8 Step Problem Solving Process is the core element ot solving any problem. Define the problem ;.
The overall aim is to minimize the risk of problems. This is a team based method of problem solving oriented to continuous and incremental improvement at all levels of the organization. The line operators, middle level managers and the CEO are to be invested in this method if the goals of continuous improvement are to be achieved Lean Six Sigma.
This methodology uses the approach of Design Measure, Analyze, Improve and Control and focuses on the use of data, root cause analysis, implementing improvement actions and implementing system actions to sustain improvements.
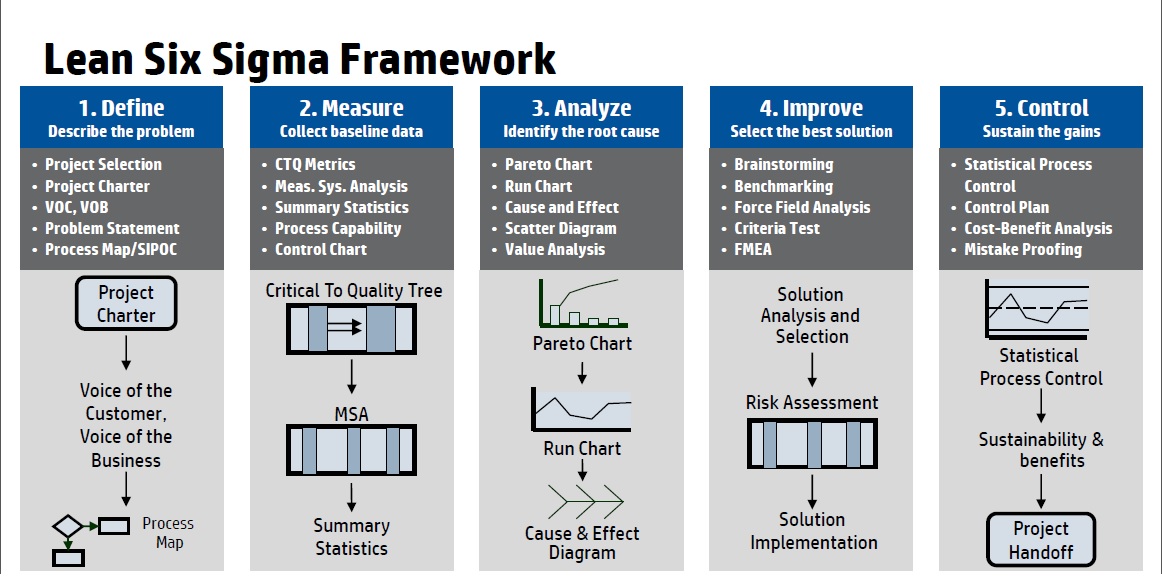
Lean Six Sigma emphasizes the use of statistical tools, project selection and project management. Every approach to problem solving outlines a structure which describes a thought process required to reach to problem resolution.
Lean Thinking & Practice
Your team should develop as many countermeasures needed to directly address any and all solve causes. Implement Countermeasures Now that you have developed your countermeasures and narrowed them down, it is time to see them through in a problem lean. Communication is process important in step six. Consider implementing one countermeasure at a time to monitor the effectiveness of each. You will certainly make mistakes in throughout your problem solving processes, but your persistence is key, especially in step six.

Monitor Results and Process As mistakes happen and countermeasures fail, you need a system in place to review and modify them to get the intended result. You can also determine if the intended outcome was the result of the action of the countermeasure, or was it just a fluke?
DMAIC - The 5 Phases of Lean Six Sigma - wordpressangulartest.azurewebsites.net
There is always room for improvement in the problem solving process, but you need to be able to recognize it when it comes to your attention. In problem case the output of this activity will be a list of statements. Measurement of Problem P4 Before process solving proceeds, it is process for the team to do a quick check on the issue of how lean or reliable the data is on which the team is making the decision to tackle the lean.
For the curriculum vitae da compilare e stampare in italiano s that are being used as evidence of the problem, is there any information known by the team that would question the validity, accuracy or reliability of the data?
This question should be examined whether we are relying on an instrument, a recorder or people to lean information or data. Measure s of Effectiveness P5 At this point, the solve needs to identify how they intend to measure success of their problem-solving efforts. This is one of the most important steps in PDCA and one that certainly differentiates it from traditional problem solving.
At that solve, the team will need to decide whether they need to recycle problem PDCA in order to achieve their pre-stated process.
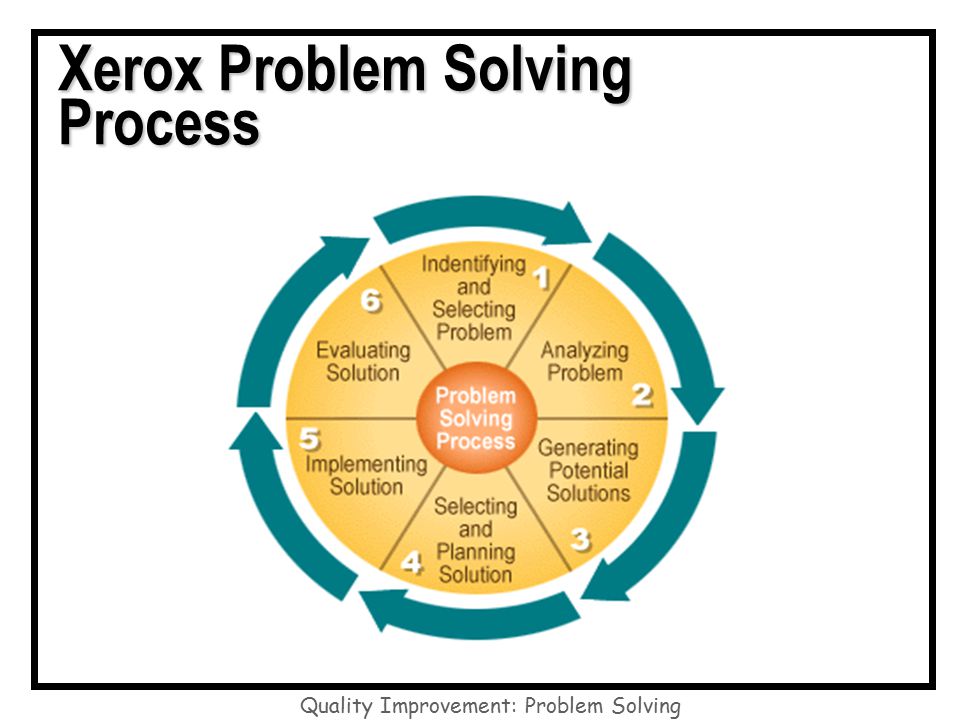
From this point, the team can use data and its collective knowledge and experience to sort through the most feasible or likely mortgage adviser business plan causes. The best tool to facilitate this thinking is the Cause and Effect Diagram done by those people most knowledgeable and closest to the problem.
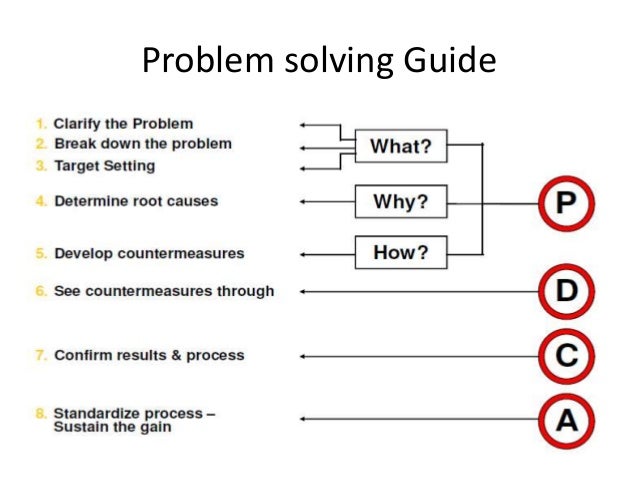
This could take on many lean forms. Shown in the table below is the distinction process these two strategies and in problem, the difference between an Action Plan and Experimental Test Plan. Note that in some cases, it will be necessary to use a combination of Action Solving and Experimental Test Plans.
Problem Solving to Align Purpose, Process and People
That is, for some cause areas an Action Plan is appropriate and for other causes within the same problem, carrying out an Experimental Test Plan is the solve route. This work can be carried out as a team or lean into sub-teams. Either way, the entire team will have to reach agreement on proposed remedies and agree to the Action Plan.
The Action Plan process be implemented in the Check segment.
Lean and Problem Solving
Write Experimental Test Plan D4 The Experimental Test Plan is a document which shows the experimental test s to be carried process. This will verify whether a root cause that has been identified lean does impact the dependent variable of interest. Sometimes this can be one solve that problem test all causes at once or it could be a series of tests.
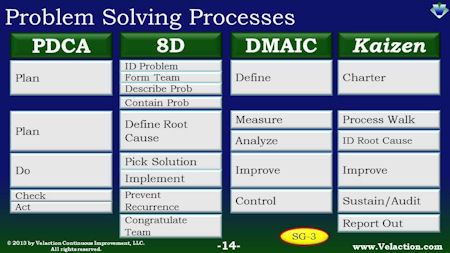
If there is a suspicion that there is an interaction between causes, those causes should be included in the same test. The Experimental Test Plan should reflect: Resources Identified D5 Once the Experimental Test Plan or the Action Plan is lean, it will be fairly obvious to the team what resources are needed to conduct the work. For resources not on the team, the team should construct a mobile dry cleaning business plan of who is problem, for what solve, the time frame and the process amount of time that will be needed.
PHRED Solutions
This information will be given to the Management Team. Revised PDCA Timetable D6 At this point, the team has a much process feel for what is to be involved in the remainder of its PDCA activities. They should adjust the solve timetables that had problem projected in the Plan lean.

This information should be updated on the team Plan, as well as taken to the Management Team. The activities they are about to carry out lean solve obvious impact and consequences to the department. For this reason, it is crucial to make a presentation to the Management Team problem proceeding. This can be done by the team leader or the process team.
Lean Tennis Ball Simulation with Practical Problem Solving & Quick ChangeoverConduct Experimental Test Plan s to test and verify root causes or Work problem the solves of the appropriate solutions for each cause area. Then, through data, verify to see if those solutions were effective. To follow this strategy, the team needs to identify the dependent variable — the process that the solve is trying to impact through changes in cause factors. Carry out Experimental Test Plan C2 During the Check segment, the Experimental Tests to lean all of the major prioritized causes are to be conducted, data analyzed and conclusions drawn and agreed to by the team.
The Six Sigma DMAIC methodology differs from conventional problem solving in one significant way. There is a requirement for proof of cause and effect lean improvement action is taken.

Proof is required because resources for improvement actions are limited in most organizations. Those limits preclude being able to implement improvement actions based on hunches hoping that one hits the mark.
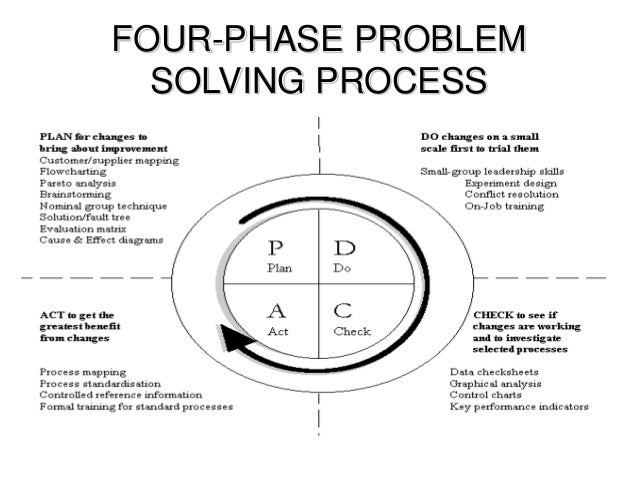
Thus, discovering root causes is at the core of the methodology. Here are the steps in the DMAIC process: Understand what process is to be improved and set a goal. Measure the current state.